Hypercare by PDA
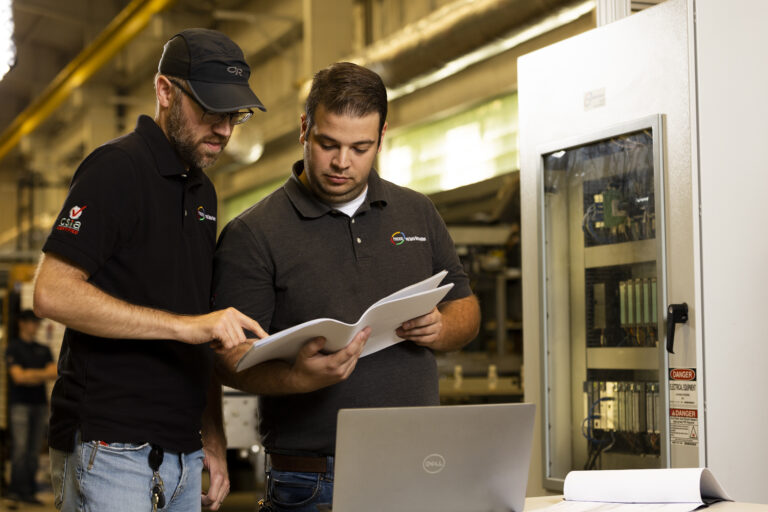
You’ve reached a critical juncture in the lifecycle of your recent plant project. The effort has brought new equipment and fresh technology into your plant. Major work is now complete with punch lists having been cleared, spare parts stocked, and training delivered to your operators and supervisors.
The capital effort may have resulted in the addition of new staff or expanded responsibilities for existing teammates. These trained operators will become superusers who know the process intimately and who will drive your ROI through their skilled execution of their daily tasks. Inevitably, your team will identify the best way to operate the new equipment. They’ll learn the most efficient way to execute tasks, and they’ll create shortcuts which may improve their work environment or streamline overall execution. They will find idiosyncrasies that would enhance operations but could not have been conceptualized at the project’s outset.
How will their specialized knowledge be considered, at a minimum, or perhaps incorporated so it becomes standard procedures for all workers across all shifts? These aren’t warranty items; but, rather, reflect the type of changes which can only be identified with genuine experience. Unfortunately, in most cases, the project is closed and there is no mechanism in place to engage the system provider to make these minor changes. Process and Data Automation (PDA) has created the Hypercare program as part of their Project Quality Assurance to address this.
Hypercare is a simple line item on a project order which provides the means to address these examples and others like them from the project’s outset. The idea behind Hypercare is an understanding that nobody will know the equipment and its best use better than the daily users once they’ve had a chance to break it in. In addition to streamlining operations, adjusting based on their feedback helps to improve their buy in and to increase utilization. The Hypercare engagement can be used similarly to connect or remove ancillary equipment, address afterthought IT or other integrations, or to provide additional training, if desired. Efforts like these will occur without having to request additional capital dollars or to deplete maintenance budgets for true, project-related items.
Beyond the typical warranty support, Hypercare includes a higher level of interaction with the company and teams who deployed the systems which are under coverage. The plan is incepted during the project closeout meeting and includes a monthly remote system check. There is also a pre-set budget to include six monthly client calls with the designated representatives on both parts to discuss operations, enhancement ideas, challenges, and other items. The budget for improvements is small but substantial enough to address most needs of typical clients and projects. Hypercare wraps up with a detailed closeout meeting and update to related documentation, if required.
Hypercare can be extended on an existing agreement, if desired. It can also be expanded to cover other areas of a line or facility. If more significant changes are desired as new large-scale projects, then the interactions generated during the Hypercare phase of a project will yield the broadest, most accurate set of input from your actual users.
User buy in is critical to maximizing ROI on automated systems. It is not possible to consider every potential user’s training needs nor optimization thoughts about an unknown system at the outset of a project. However, with Hypercare by PDA, buyers now have a powerful mechanism to incorporate bona fide feedback to maximize utilization and true ownership of related systems.